Development of Flapping Wings of Bird
Info: 13581 words (54 pages) Dissertation
Published: 10th Dec 2019
Tagged: Animal Sciences
ABSTRACT | I | |
LIST OF FIGURES | II | |
Page No. | ||
CHAPTER-1 | INTRODUCTION | 1 |
CHAPTER-2 | LITERATURE REVIEW | |
2.1 UNIVERSITY OF TORONTO MODEL | 6 | |
2.2 DELFLY | 8 | |
2.3 HARVARD UNIVERSITY OF ROBOBEE | 10 | |
2.4 WING DESIGN | 12 | |
2.6 MECHANISM | 15 | |
2.7 GEARS AND GEAR TRAINS | 17 | |
2.8 LINKAGES | 23 | |
2.9 D.C.MOTOR | 27 | |
2.10 ARC WELDING | 34 | |
CHAPTER-3 | DESIGN AND SELECTION OF PARTS | |
3.1 BODY | 38 | |
3.2 WINGS | 39 | |
3.3 HINGE | 40 | |
3.4 DRIVE TRAIN | 40 | |
3.5 BATTERY | 43 |
3.6 MOTOR | 44 | |
CHAPTER-4 | MANUFACTURING OF PARTS | |
4.1 WING SPARS | 46 | |
4.2 BODY | 47 | |
4.3 ARC WELDING | 47 | |
4.4 FINAL ASSEMBLY | 47 | |
CHAPTER-5 | CONCLUSIONS | 49 |
BIBLIOGRAPHY 50 |
- Figure 1.1 AIR LOAD 2
- Figure 1.2 LILIENTHAL MODEL 3
- Figure 1.3 QUILL STRUCTURE 4
- Figure 2.1 TORONTO MENTOR PROJECT 6
- Figure 2.2 DELFLY 8
- Figure 2.3 DELFLY DRIVE TRAIN 9
- Figure 2.4 CLAP AND FLING 11
- Figure 2.5 HARRIS MODEL 15
- Figure 2.6 THREE PANEL MODEL 15
- Figure 2.7 SPUR GEARS 19
- Figure 2.8 GEAR ENGAGE 21
- Figure 2.9 GEAR TERMINOLOGY 22
- Figure 2.10 WINDSHIELD WIPER 25
- Figure 2.11 FOUR BAR LINKAGE
- Figure 2.12 D.C.MOTOR 29
- Figure 2.13 THE OPERATION OF D.C. MOTOR 30
- Figure 2.14 CONSTRUCTION OF PERMANENT
- Figure 2.15 EQUIVALENT CIRCUIT OF PERMANENT
- Figure 2.16 ARC WELDING 38
- Figure 3.1 ISOMETRIC VIEW OF THE MODEL 40
- Figure 3.2 FINALIZED DRIVE TRAIN 44
- Figure 3.3 REAL MODEL (DRIVE TRAIN) 45
- Figure 3.4 LEAD ACID BATTERY USED 46
- Figure 3.5 DC MOTOR 47
- Figure 4.1 WING SPARS 48
- Figure 4.2 COMPLETE ASSEMBLY 50
Fig No. 1.1 Air load
All the existing birds' feather fly mechanism works just like the red bird shown here. What is the difference between these two birds? There are two major differences The first difference is that the shaft of the feather, represented by green circles, is always away from the bird's body for living red bird, and the opposite for the fictitious blue bird. The second difference is that, the tip flight feather of the red bird is always fully visible if we look under the bird, and the other feathers always overlap one another. For the blue bird, the feather closest the bird body is fully visible and the rest is overlapped. I call the red bird feather arrangement a positive arrangement and the blue birds a negative arrangement. Also if the shaft of the feather is away from the bird, it will be called a positive feather and will be shown as a red feather. The blue birds flight feather is similar to the shaft of the feather & is at all times closer to the bird body. These types of feathers will be so-called negative feathers positive and negative for feathers and feather arrangements.Fig No. 1.2Lilienthal model
If the feathers were performing as a flap, then why don’t we see birds in natural surroundings that be situated like the blue bird? Subsequently in two cases the flaps are unlocked in upstroke & there should be a 50/50 chance for together red and blue birds. However we do not see birds like the blue bird. Perhaps it’s because all birds, by good luck, derived from one type of bird and that is why we see only birds like red one in nature. As Lilienthal stated in his book, in nature any design is not an unintentional one. If environment chooses one design over the other, than there must be a firm intention for that. , when the feathers are opened in up stroke, the air is pushed toward under the bird’s body for the red bird, and away from the body for the blue bird. This is a vital difference.Fig No. 1.3 Quill structure
Think for a moment that the blue bird is on the ground, and a predator is approaching. The bird automatically flaps its wings to liftoff. First it is pushing its wings down, it is also pushing the air below its wing down, and it gains small elevation. But when the bird is in up stroke, the motion of the wing creates a vacuum under the wing. In the meantime the air under the wing has an outward inertia due to previous down stroke and does not have enough time to fill the gap. At the same time the air passing between the feathers going outward, blocking some of extra air coming toward under the wing; As a result the bird will be sucked downward. This will nullify all the altitude gain obtained during the wings down stroke and because it did not get enough air under the wing, the next down stroke will be fragile. The bird will uncontrollably flap its wings and fall down with each up stroke, and with each down stroke it will go up slightly. So birds that are like the blue bird could only fly if they were to jump from a branch off of a tree or from a cliff, taking off from the ground would be next to impossible for them. Now let's consider the red bird. When the wings are coming down, whatever happened with the blue bird will be repeated for the red bird as well. Though their up stroke is fairly dissimilar from blue birds. While the wings are going up, the opening in the feather will push the air under the bird’s body with a force that, not only will it will super charge the void with the air from above, it will also provide some upward force to the bird’s body and from falling downward. Also the air coming around and under the bird toward the void will be assisted by the air coming through the feathers above. I use the term super charge here, since this is closely what it is, the power used through the upstroke by the bird is converted directing more air atoms downward. It has two effects. Firstly it gives an upward lift to the bird similar to a Harrier jet. Secondly it gathers air below the wing for next downward stroke. The next downward stroke will take the bird upper. For the red bird, there are extra air atoms to be pushed downward for independently down stroke than the blue bird. Since it is supercharging air under its wing, the red bird will take off from ground very efficiently. Owing to the supercharging effect we assume the red bird’s feather organization as a positive arrangement. Feathers play a dynamic role throughout flight, both birds, red and blue, will advantage from the opening of flaps because it will reduce the drag throughout the upstroke. Supposing that both birds are flying the same speed during a travelling flight one may take up that there are no modifications between the two birds. Both birds will get fresh air underneath their wings due to their frontward speed. However, there is a slight difference between the airflow generated by the upstroke of the wings. When the blue bird’s feathers are visible in the upstroke external moving air pushes the tip of the feathers downward and tilts it in such a way that it generates an out and downward air drive. However, with the red bird this process will create a merging air flow as shown in the figure. This is very important event. As we know, when an object moves through the air with speed, it creates a low pressure region behind it, which causes drag that will reduce the speed of the moving object. Therefore the red bird’s air movement will try to fill the gap behind the bird, reducing the drag. Since the blue bird’s wings are pushing the air away from the body, it will not fill the gap behind it. This will cause considerable drag on the bird's movement. Also, the blue bird is trying to push the air outward, into still air, which might show resistance to it, and cause the bird to use more force and energy to push the air. On the other hand, the red bird wings are pushing the air toward a cavity, which needs air, so that it can be filled. In short satisfying the void behind a flying bird will decrease the drag and as a outcome energy consumption of upward moving wings will be decreased. CHAPTER 2 LITERATURE REVIEW2.1 University of Toronto Mentor
Mentor at the University of Toronto was among the first radio controlled MAV’s to achieve hover using 4 wings in a clap and fling motion, as shown below in Figure 2.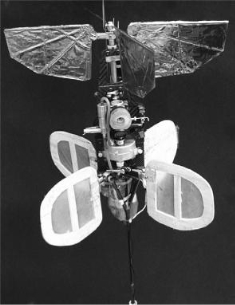
2.2 Delfly
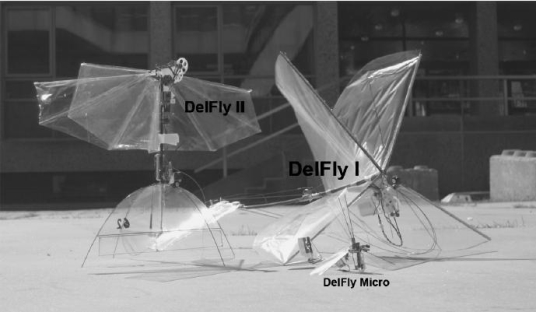
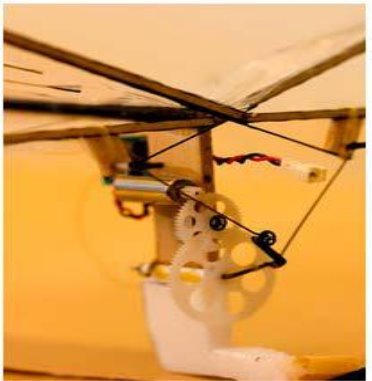
2.3 Harvard University RoboBee
Robert Wood and a team of four members at Harvard University newly developed a very small robot that very closely mimics a flapping insect. With the use of piezoelectric actuators, the wings have three degrees of freedom. The robot does not have a tail and makes its altitude changes through manipulating its wings. This is the same as how an actual insect flies and controls itself. The robot suffers from scrambling issues and the device requires external power, for no normally available power source is small enough to fit onboard. The lack of a tail and any sort of control sensor also results in unstable flight; most tests only run for a few seconds until the aircraft loses control. RoboBee is a ace of engineering, using novel contraction and manufacturing techniques; however, with a wingspan of just one inch, its scale is smaller than the scope of this project and was not heavily considered in our design.2.4 Clap and Fling
The clap and fling is a method of flapping that generates more lift than conventional flapping of wings. It can be seen being used in nature by sparrows and some species of fly. The clap and fling works by swiftly bringing two wings together beginning with the primary edge. The leading edges touch and elastic wings will follow in a sensation known as feathering. As the wings come together air is pushed out the back generating thrust, which when angled properly will create lift. When the wings are together they instantly begin to whither apart letting air to rush in from the opposite. This suction also creates thrust, pulling the wings forward. From an outside viewpoint the air is being dispersed around the wings, which creates lift under the Kutta situation. The wing is quickly moving though air causing an unsteady flow and vortices creating around the leading edge. These vortices will interrelate in ways not yet agreed with the vortices coming off the edge of the wing generating extra lift. All of these occurrence together are illustrated below.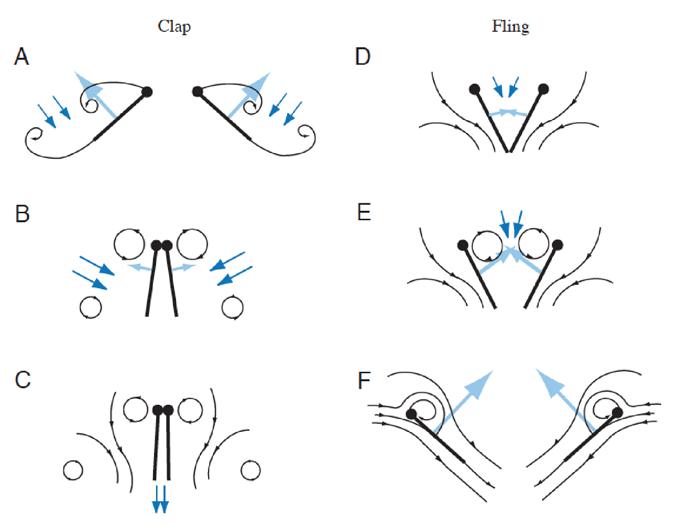
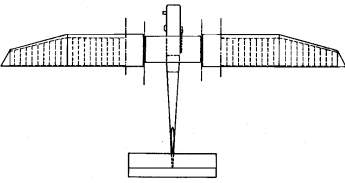
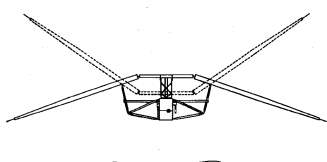
Types of Mechanisms
From the period of Archimedes mechanisms were well-thought-out to be constructed from simple machines, such as the lever, pulley, screw, wedge, wheel and inclined plane. It was Reuleaux who focused on bodies, called links, and the connections between these bodies called kinematic joints or pairs. In order to use geometry to study the drive of a mechanism, its links are modeled as inelastic bodies. This means distances in the middle of points in a link are assumed to be unaffected as the mechanism moves that is the link does not bend. Thus, the relative movement in the middle of points in two connected links is considered to result from the kinematic pair that joints them. Kinematic pairs are measured to provide ideal constraints in the middle of two links, such as the constraint of a single point for pure rotation. The constraint of a line for pure sliding, as well as pure rolling lacking slipping and point contact with slipping. A mechanism is modeled as an assembly of inelastic links and kinematic pairs.Kinematic pairs
Reuleaux stated the ideal connections in the mid of links kinematic pairs. He distinguished in the middle of higher pairs which were said to have line contact among the two links and lower pairs that have area contact amid the links. J. Phillips shows that there are many approaches to build pairs that do not fit this simple. A lower pair is a joint that has surface interaction amid the pair of elements. We have the following cases:- A revolute pair requires a line in the moving body to remain co-linear with a line in the fixed body, and a plane vertical to this line in the moving body maintains contact. It imposes five constraints on the relative movement of the links, which hence has one degree of freedom.
- A prismatic joint requires a line in a moving body remain co-linear with a line in the fixed body, and a plane similar to this line in moving body sustain contact with a alike parallel plane in the immovable body. This enforces five constraints on the relative movement of the links, which consequently has one degree of freedom.
- A cylindrical joint needs a line in the moving body to remain co-linear with a line in the fixed body. It is a blend of revolute joint and sliding joint. This joint has two degrees of freedom.
- A ball joint, desires that a point in the moving body keep connection with a point in the static body. This joint has three degrees of freedom.
- A planar joint needs that a plane in the moving body maintain contact with a plane in fixed body. This joint has three degrees of freedom.
- A helical joint has one degree of freedom since the rotational indications are related to the helix angle of the thread.
Planar mechanism
It is a mechanical system which is held in reserve so the paths of points in all the bodies of the method fib on planes parallel to the ground plane. The revolving axes of hinged joints that join the bodies in the system are perpendicular to this ground plane.Spherical mechanism
It is a mechanical system that the bodies change in a way that the paths of points in the system lie on concentric spheres. The rotating axes of hinged joints that associate the bodies in the system to pass through the center of these spheres.Spatial mechanism
It is a mechanical system which has at least one body that moves in a direction that its point trajectories are general space curves. The turning axes of hinged joints that connect the bodies in the system form lines in space that do not transect and have different joint normals.2.7 Gears and gear trains
- The ratio of pitch circles of coupling gears states the speed ratio and the mechanical use of the gear set.
- A planetary gear train provides high gear reduction in a compact package.
- It is possible to design gear teeth for gears that are not-circular, but still transmit torque smoothly.
- The speed ratio of chain and speed ratio of belt drive is calculated in the same way as gear ratios. See bicycle gearing.
History of the differential gear
The earliest gears was Chinese actual examples of wheels and moulds for wheels dating from the 4th century B.C. which have been preserved. It might be remarked that these "machine" gear wheels are characterized by having a "round number" of teeth and a shank with a square hole which fits without turning on a squared shaft.[3] The earliest gears in Europe was circa A.D. 50 but they can be drawn back to the Greek mechanics of the Alexandrian school in the 3rd century BCE and were greatly settled by the Greek polymath Archimedes (287–212 BCE). The Antikythera mechanism is a model of a very early and complex geared device, designed to compute astronomical positions. Its time of building is projected between 150 and 100 BC.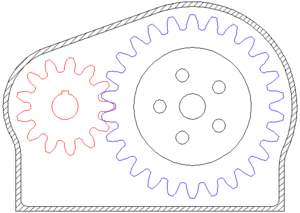
General nomenclature
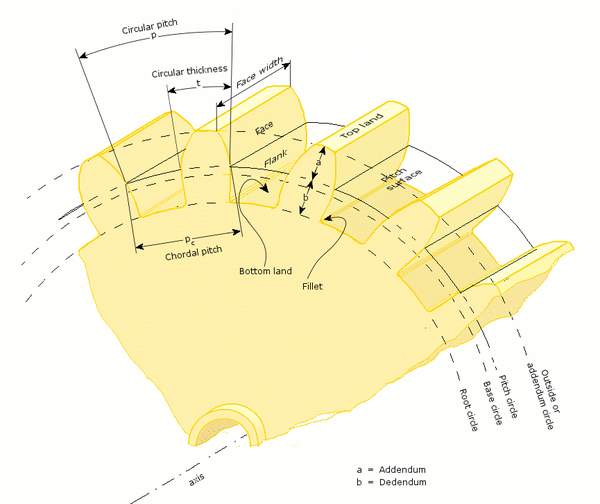
- Rotational frequency, n:
- Angular frequency, ω:

- Number of teeth, N:
- Gear, wheel:
- Pinion:
- Path of contact:
- Line of action, pressure line:
- Axis:
- Pitch point:
- Pitch circle, pitch line:
- Pitch diameter, d:

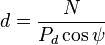
- Module or modulus, m:



Cam and follower mechanisms
A cam and a follower is molded by the direct contact of two permanent shaped links. The driving link is called the cam and the link that is driven by the direct contact of the surface of both links is called the follower. The form of the mating surfaces of the cam and follower controls the motion of the mechanism. Generally a cam and follower mechanism's energy is conveyed from cam to follower. The cam shaft is rotated according to the cam profile while the follower moves up and down. Diverse types of eccentric cam followers are also available in which energy is conveyed from the follower to the cam. The main advantage of this type of cam follower mechanism is that the follower moves a tiny bit and helps to rotate the cam 6 times extra circumference span with 70% force.2.8 Linkages
A linkage is a collection of links connected by joints. The links are the structural elements and the joints let motion. The single most useful example is the planar four-bar linkage. Though, there are many more special linkages:- Watt's linkage is a four-bar linkage that generates a rough straight line. It was serious to the operation of his design for the steam engine. This linkage acts in vehicle suspensions to prevent side movement of the body comparative to the wheels.
- The achievement of Watt's linkage leads to the design of similar straight-line linkages.
- The Peaucellier linkage produces a true straight-line output from a rotary input.
- The Sarrus linkage is a spatial linkage that generates straight-line movement from a rotary input.
- Jansen’s linkage and the Klann’s linkage are new inventions that deliver stimulating walking actions. They are individually a six-bar and an eight-bar linkage.
Flexure mechanisms
A flexure mechanism contains a series of inelastic bodies connected by accommodating elements that is designed to produce a geometrically well-defined motion upon claim of a force. Linkage Mechanism Have you ever wondered what kind of mechanisms causes the wind shield wiper on the front widow of car to oscillate. The mechanism, shown in Figure, transforms the rotary motion of the motor into an oscillating motion of the windshield wiper.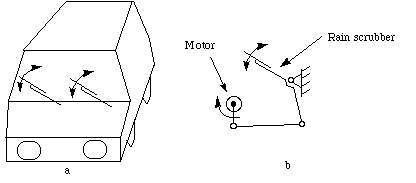
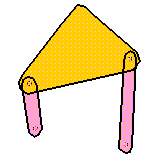
- Continuous, with a constant or variable angular velocity ratio. rotation into continuous rotation
- Continuous rotation into oscillation or reciprocation (or the reverse), with a constant or variable velocity ratio.
- Oscillation, reciprocation with a constant or variable velocity ratio.
- Function generation: The relative motion in the middle of the links connected to the frame.
- Path generation: The track of a tracer point.
- Motion generation: The motion of the coupler linkage.
- The four-bar linkage mechanism, and
- The slider-crank mechanism.
- Crank: An adjacent link which revolves relative to the frame.
- Rocker: Any link which does not revolve.
- Crank-rocker mechanism: In a four bar linkage where shorter side link revolves and the other one oscillates.
- Double-crank mechanism: In a four bar linkage where both of the side links revolve.
- Double-rocker mechanism: In a four bar linkage if both side links rock.
- s = length of shortest bar
- l = length of longest bar
- p, q = lengths of intermediate bar
- When the smallest link is a side link then the mechanism is a crank-rocker mechanism. The smallest link is the crank in the mechanism.
- When the smallest link is the frame of the mechanism then the mechanism is a double-crank mechanism.
- When the shortest link is the coupler link, the mechanism is a double-rocker mechanism.
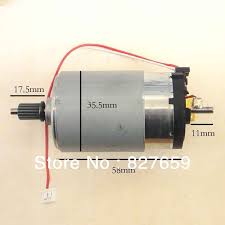
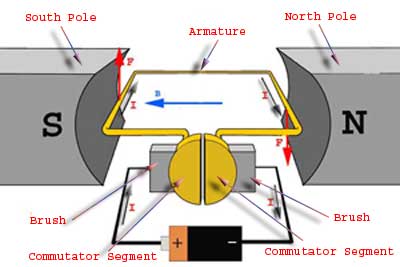
Working Principle of Permanent Magnet DC Motor or PMDC Motor
As we said earlier the working principle of PMDC motor is just similar to the general working. That is when a carrying conductor comes inside a magnetic field, a mechanical force will be experienced by the conductor and the direction of this force is governed by Fleming’s left hand rule. Like in a permanent magnet dc motor, the armature is placed inside the magnetic field of permanent magnet; the armature is rotated in the direction of the generated force. Here each conductor of the armature experiences the mechanical force F = B.I.L Newton where B is the magnetic field strength in Tesla (weber / m2), I is the current in Ampere flowing through that conductor and L is length of the conductor in metre comes under the magnetic field. Each conductor of the armature experiences a force and the compilation of those forces produces a torque, which tends to rotate the armature.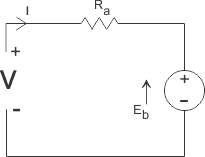
Fig No. 2.15 Equivalent Circuit of Permanent Magnet DC Motor or PMDC Motor
As in PMDC motor the field is produced by permanent magnet, there is no need of drawing field coils in the equivalent circuit of permanent magnet dc motor. The supply voltage to the armature may have armature resistance drop and rest of the supply voltage is opposed by back emf of the motor. Hence voltage equation of the motor is given by,
- No need of field excitation arrangement.
- No input power in consumed for excitation which improves efficiency of dc motor.
- No field coil hence space for field coil is saved which reduces the overall size of the motor.
- Cheaper and economical for fractional kW rated applications.
Disadvantages of Permanent Magnet DC Motor or PMDC Motor
- In this situation, the armature reaction of DC motor may not be compensated so the magnetic strength of the field can become weak due to the demagnetizing outcome of armature reaction.
- There is also a chance of getting the poles permanently demagnetized (partial) due to excessive armature current during starting, reversal and overloading condition of the motor.
- Another key drawback of PMDC motor is that, the field in the air gap is fixed and limited and it cannot be controlled externally. Therefore, very efficient speed control of DC motor in this type of motor is difficult.
Applications of Permanent Magnet DC Motor or PMDC Motor
PMDC motor is extensively used where small dc motors are required and also very effective control is not required, such as in automobiles starter, toys, wipers, washers, hot blowers, air conditioners, computer disc drives and in many more. 2.10 WELDING Arc welding Arc welding is a process which is used to join metal and metal by using electricity to create adequate heat to melt metal, and the melted metals when cool result in a binding of the metals. It is a type of welding that uses a welding power supply to create an electric arc between an electrode and the base material to melt the metals at the welding point. They can be used as either direct (DC) or alternating (AC) current, and consumable or non-consumable electrodes. The welding region is usually protected by some type of shielding gas, vapor, or slag. Arc welding processes can be manual, semi-automatic, or fully automated. First developed in the late part of the 19th century, arc welding became commercially important in shipbuilding during the Second World War. Today it remains as an vital process for the assembly of steel structures and vehicles. To supply the electrical energy necessary for arc welding processes, a number of different power supplies can be used. The most common grouping is constant current power supplies and constant voltage power supplies. In arc welding, the voltage is directly related to the length of the arc, and the current is related to the amount of heat input. Constant current supply is broadly used in manual welding processes like gas tungsten arc welding and shielded metal arc welding, because they maintain a relatively constant current even as the voltage varies. This is important because in manual welding, it can be difficult to hold the electrode perfectly steady, and as a result, the arc length and thus voltage tend to fluctuate. Constant voltage power supply keep the voltage constant and vary the current, and as a result, are mostly used for automated welding processes such as gas metal arc welding, flux cored arc welding, and submerged arc welding. In this process arc length is kept constant, so that any fluctuation in the distance between the wire and the base material is quickly resolved by a huge change in current. In case, if the wire and the base material get very close, the current rapidly increases and in turn causes the heat to increase and the tip of the wire melts and returns to its original separation distance. The direction of current used in arc welding plays a significant role in welding. Consumable electrode processes like shielded metal arc welding and gas metal arc welding regularly use direct current, but the electrode can be charged either positively or negatively. In welding, the positively charged anode has a larger heat concentration (around 60%) and, as a result, changing the polarity of the electrode affects weld properties. If the electrode is positively charged, it melts quickly, increasing weld penetration and welding speed. Alternatively, a negatively charged electrode results in thin welds. Non-consumable electrode processes, like gas tungsten arc welding, can use any type of direct current (DC), as well as alternating current (AC). However with direct current the electrode only creates the arc and does not provide filler material, a positively charged electrode causes shallow welds, while a negatively charged electrode makes deeper welds. Alternating current rapidly moves between these two, which results in medium-penetration welds. One disadvantage of AC, a fact that the arc requirement be re-ignited after every zero crossing, has been addressed with the invention of special power units that produce a square wave method instead of the normal sine wave, removing low-voltage time after the zero crossings and minimizing the effects of the problem.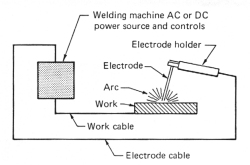

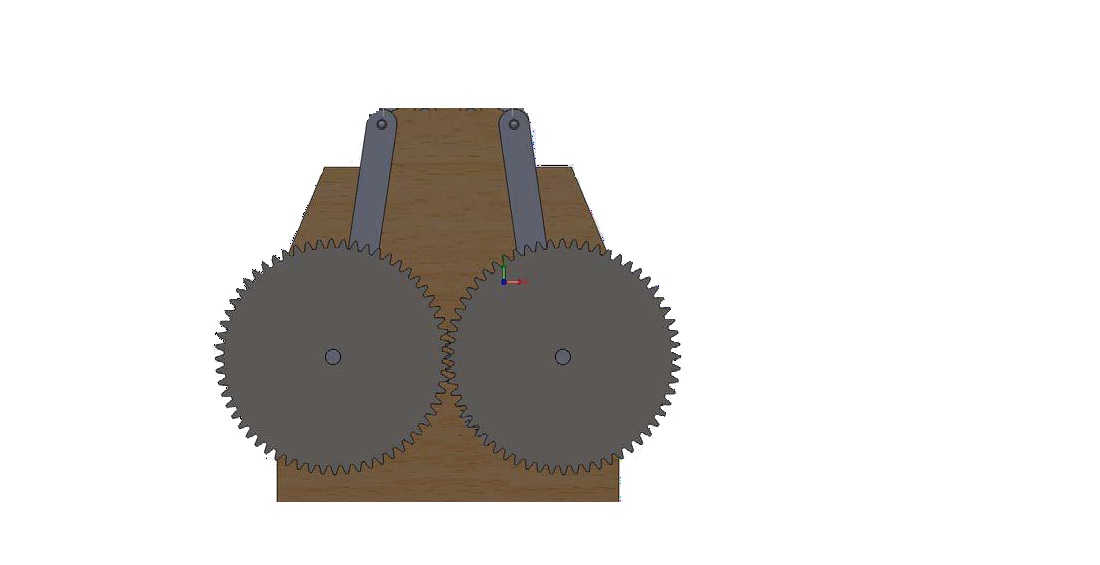
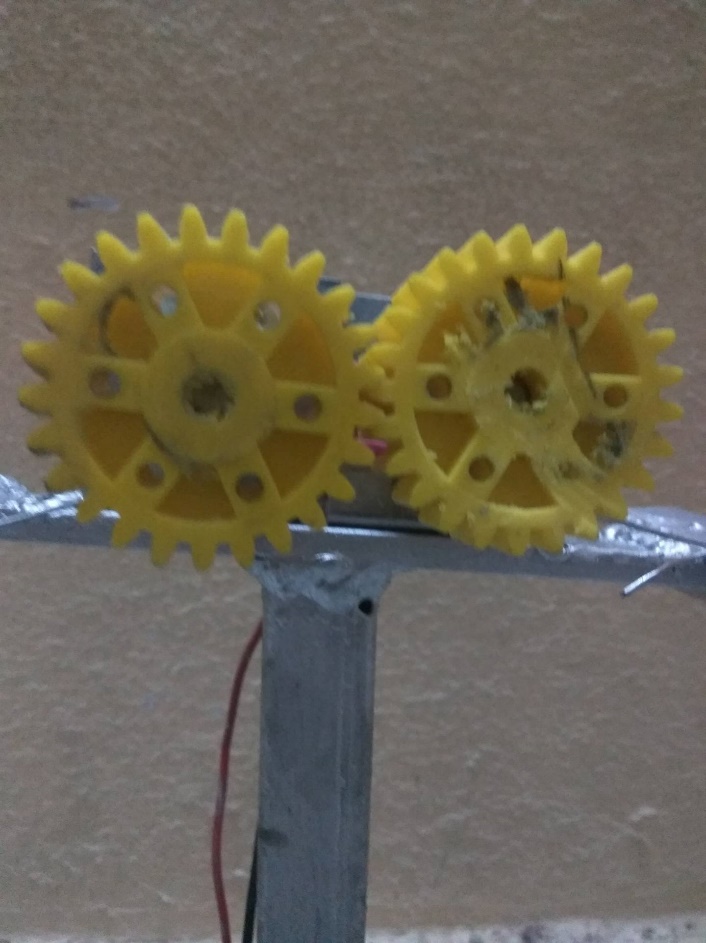
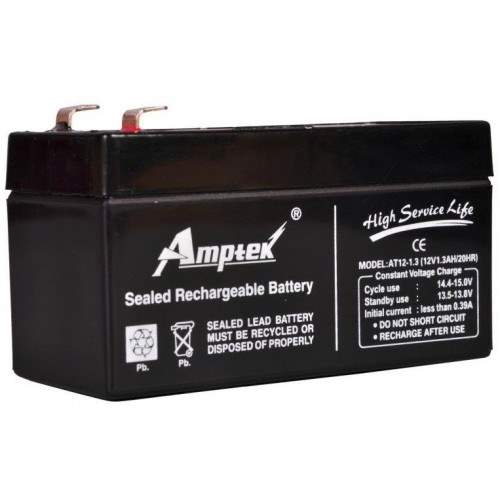
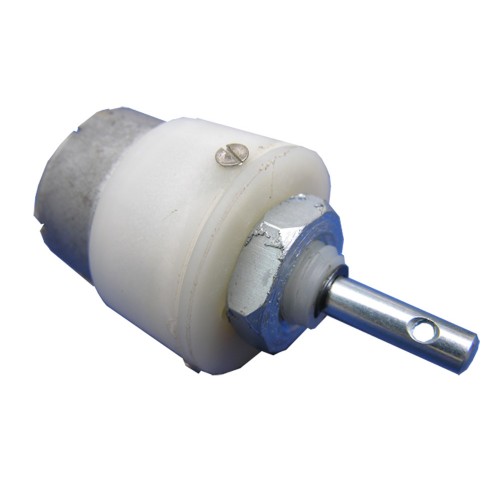
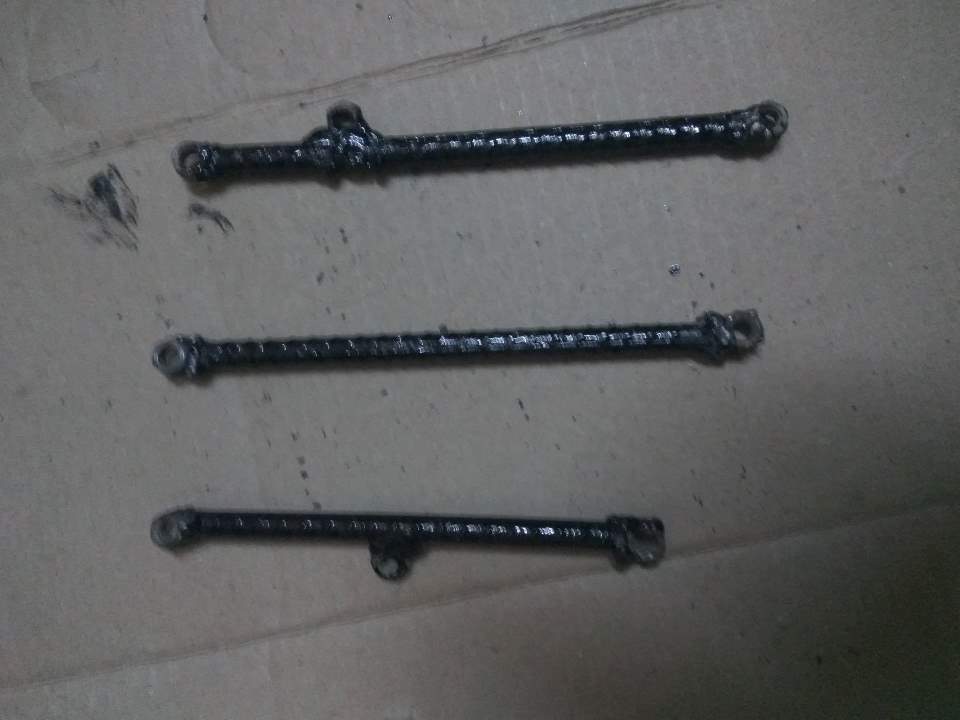
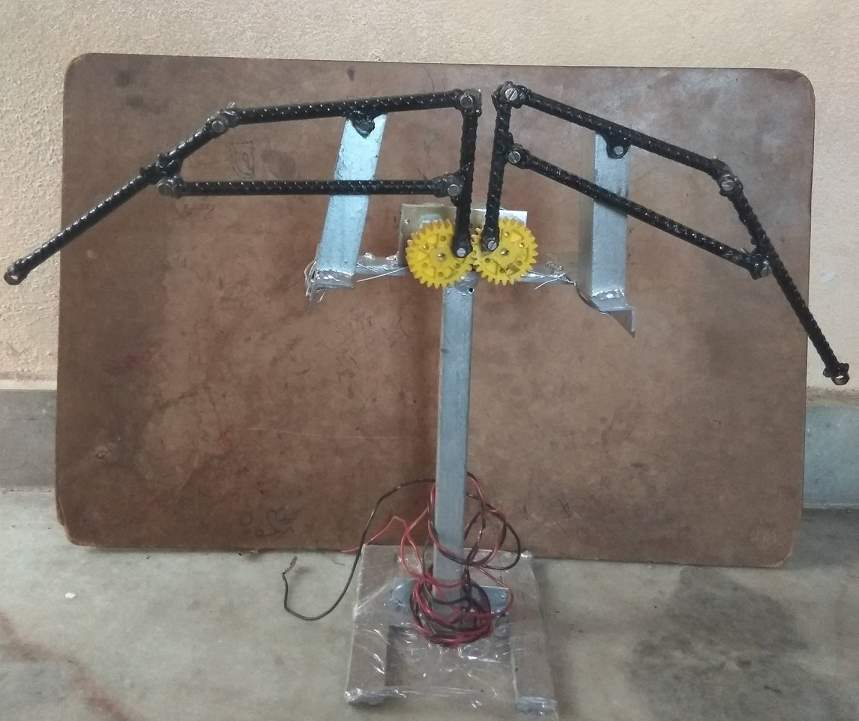
- Agrawal, S. K., Madangopal, R., & Khan, Z. A. (2004). Biologically inspired design of small flapping wing air vehicles using four-bar mechanisms and quasi-steady aerodynamics. Journal of Mechanical Design, , 1-8.
- Bruggeman, B. (2010). Improving flight performance of DelFly II in hover by improving wing design and driving mechanism. Delft University of Technology M.Sc.Thesis,
- De Croon, G., De Clercq, K., Ruijsink, R., Remes, B., & De Wagter, C. (2009). Design, aerodynamics, and vision-based control of the DelFly. International Journal of Micro Air Vehicles, 1(2), 71-97.
- GAJBHIYE, S., UPADHYAY, S., & HARSHA, S. (2012). FREE VIBRATION ANALYSIS OF FLAT THIN MEMBRANE. International Journal of Engineering Science, 4
- Groen, M. (2010). PIV and force measurements on the flapping-wing MAV DelFly II. Delft University of Technology M.Sc.Thesis,
- Hara, N., Tanaka, K., Ohtake, H., & Wang, H. O. (2009). Development of a flying robot with a pantograph-based variable wing mechanism. Robotics, IEEE Transactions on, 25(1), 79-87.
- Harmon, R. L. (2008). Aerodynamic modeling of a flapping membrane wing using motion tracking experiments ProQuest.
- Krashanitsa, R. Y., Silin, D., Shkarayev, S. V., & Abate, G. (2009). Flight dynamics of a flapping-wing air vehicle. International Journal of Micro Air Vehicles, 1(1), 35-49.
- Maxworthy, T. (1981). The fluid dynamics of insect flight. Annual Review of Fluid Mechanics, 13(1), 329-350.
- Michelson, R. C. (2004). Novel approaches to miniature flight platforms. Proceedings of the Institution of Mechanical Engineers, Part G: Journal of Aerospace Engineering, 218(6), 363-373. 29
- Miller, L. A., & Peskin, C. S. (2005). A computational fluid dynamics ofclap and fling'in the smallest insects. Journal of Experimental Biology, 208(2), 195-212.
- Mueller, D., Bruck, H., & Gupta, S. (2010). Measurement of thrust and lift forces associated with drag of compliant flapping wing for micro air vehicles using a new test stand design. Experimental Mechanics, 50(6), 725-735.
- Pornsin-Sirirak, T. N., Lee, S., Nassef, H., Grasmeyer, J., Tai, Y., Ho, C., & Keennon, M. (2000). MEMS wing technology for a battery-powered ornithopter. Paper presented at the Micro Electro Mechanical Systems, 2000. MEMS 2000. the Thirteenth Annual International Conference on, 799-804.
- Sane, S. P. (2003). The aerodynamics of insect flight. The Journal of Experimental Biology, 206(23), 4191-4208.
- Shyy, W., Aono, H., Chimakurthi, S., Trizila, P., Kang, C. K., Cesnik, C., & Liu, H. (2010). Recent progress in flapping wing aerodynamics and aeroelasticity. Progress in Aerospace Sciences, 46(7), 284-327.
- Taylor, G. K. (2001). Mechanics and aerodynamics of insect flight control. Biological Reviews, 76(4), 449-471.
- Whitney, J., & Wood, R. (2012). Conceptual design of flapping-wing micro air vehicles. Bioinspiration & Biomimetics, 7(3), 036001.
Cite This Work
To export a reference to this article please select a referencing stye below:
Related Services
View allRelated Content
All TagsContent relating to: "Animal Sciences"
Animal science can be described as studying the biochemistry, physiology, and behaviour of animals that are under human control. Historically, animal science degrees were known as animal husbandry and focused on livestock. Studies now include companion animals such as cats and dogs.
Related Articles
DMCA / Removal Request
If you are the original writer of this dissertation and no longer wish to have your work published on the UKDiss.com website then please: